Simplifying Inhaler Manufacturing for a Sustainable Future
Innovative tablet-based MDI technology for rapid reformulation with low-GWP propellants.
Facing Pressure to Eliminate HFA Propellants?
Our mission is to support pharmaceutical partners in creating patient-centric, eco-conscious inhaler systems that meet evolving industry standards.
- Regulatory mandates are phasing out high-GWP inhalers
- Reformulation is slow, complex, and expensive
- IP protection is limited
Respitab
This propellant dispersible tablet is a cost-effective and innovative manufacturing platform, which enables transition to the next generation pMDI’s for a range of API’s and combination products.
Respitab offers
- Simplified manufacturing
- Rapid screening & formulation
- Strong patent protection
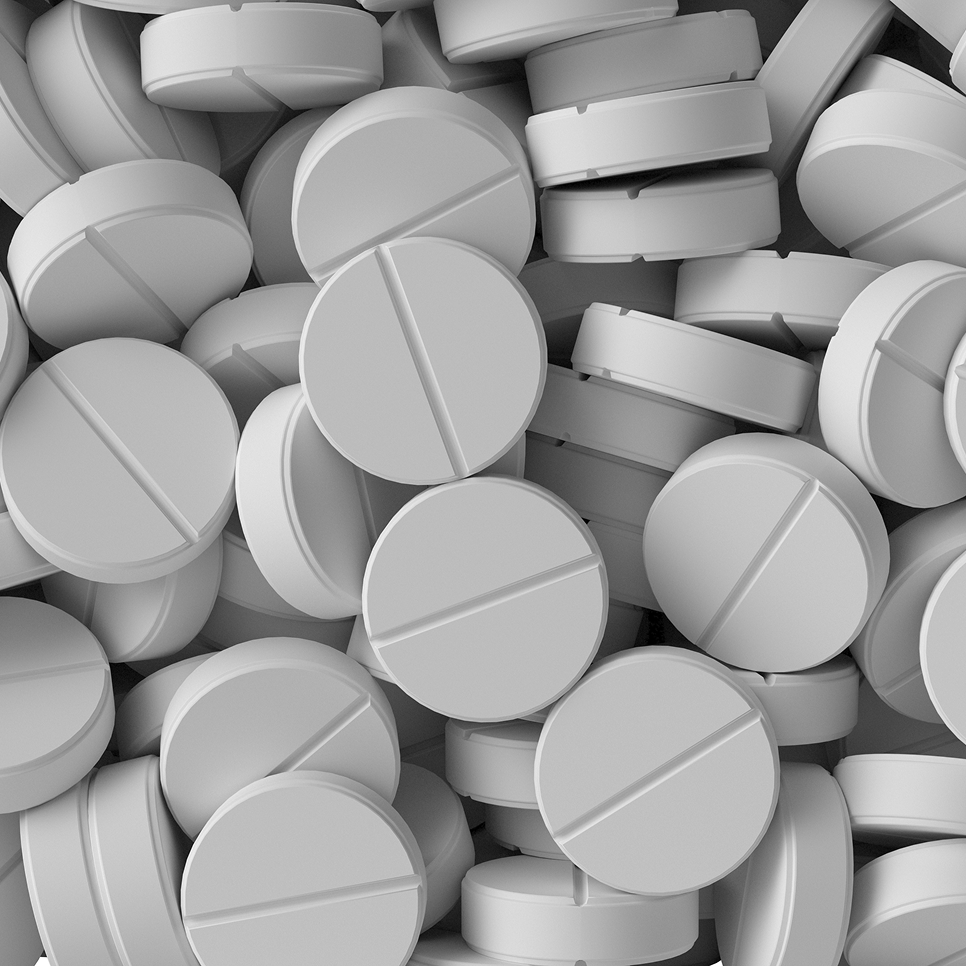
Tablet Advantages
- Flexible manufacturing with standard equipment
- No requirement for homogenization / mixing vessels
- No pressure vessel = no propellant top-up during filling
- Bulk tablets complying with release specifications
- Flexibility of batch sizes
- Ease of scalability
- Manufacturing sequence transferable to other sites
- Simplied manufacturing and cleaning processes
- Reduced waste & API losses
- Economical pathway to full commercialisation